For many decoration manufacturers, traditional cork sheets and rolls are the only option they know – and they’re great for cutting simple shapes. However, when it comes to creating custom forms and intricate details, you need natural cork in a more flexible form. That’s when a ready-to-use, dry, loose granulated cork for pressure molding comes into play. You’ll leap ahead of the competition – they haven’t even heard of it yet!
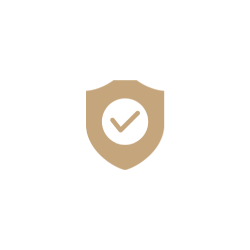
Complete Control
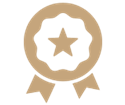
Creating Any Shapes
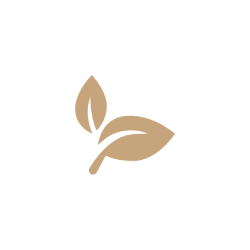
Eco-Friendly Solution
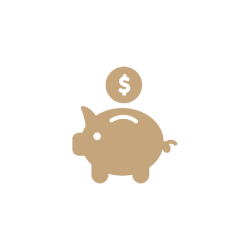
Cost-Saving
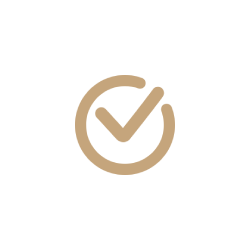
Product Consistency
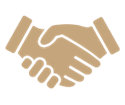
Stability
You probably have a few questions, so we’ve prepared the answers!
WHAT IS CORK MIX USED FOR?
Cork mix is used for pressure moulding cork. It’s ideal for producing components with custom shapes, such as in construction, furniture making, footwear, sports, or decorations. It’s perfect wherever unique shapes and precision are key.
HOW DOES THE CORK GRANULE FORMING PROCESS WORK?
The process involves binding small cork pieces into a solid shape using pressure and high temperature (adhesive activation occurs at 110–130°C).
Cork granules are placed into a mould, which is heated while high pressure is applied. The adhesive activates, bonding the cork granules into a cohesive whole. Once removed from the mould, the product is ready for use.
WHAT IS THE OPEN TIME OF MOULDING CORK MIX?
Cork mix doesn’t have an open time, which is one of its greatest advantages. The adhesive only activates when it reaches its activation temperature (110–130°C). This gives you full control over the moulding process – allowing you to work at your own pace without any rush.
DOES GRANULATED CORK MIX CONTAIN POLYURETHANE?
No, the adhesive in the granules is eco-friendly. The mix is free from polyurethane and solvents.
WHAT SHOULD I PAY ATTENTION TO WHEN PRESSURE MOULDING CORK GRANULES?
Pay special attention to two key aspects:
- Even distribution of granules – ensure the granules are spread evenly within the mould to avoid defects in the final product.
- Proper temperature – check that the mould reaches the required temperature range of 110–130°C. If the temperature is too low, the adhesive won’t activate.
HOW SHOULD MOULDING CORK MIX BE STORED, AND FOR HOW LONG?
Cork granules can be stored indefinitely, provided they are sealed in airtight packaging. Without proper sealing, the granules absorb moisture from the air, which can degrade their quality.
For best results, store the mix in a dry location with air humidity levels no higher than 40–50%.
CAN THE CORK MIX BE COLOURED?
Yes, cork mix can be coloured using pigments.
A common mistake is adding too much pigment at once, which can result in uneven colouring. It’s better to add it gradually, mixing thoroughly each time to ensure uniform distribution.
IS CORK GRANULE SUITABLE FOR RECYCLING?
Yes, natural cork is 100% recyclable. You can grind it down and reform it through pressure moulding, creating a new product without generating waste or extra costs!
HOW IS CORK GRANULE MADE?
Granulated cork is created by breaking down the bark of the cork oak tree into small pieces. This process transforms the natural material into a loose mix, ready for further moulding.
Time is money, and every production error means a loss of resources and customer trust. Natural cork minimises production downtime, reduces waste, and reinforces your company’s reputation as a reliable partner.
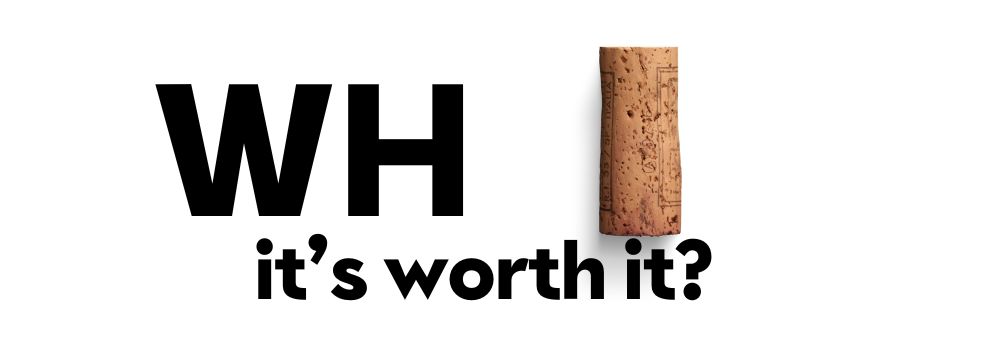
#1 NATURAL CORK = A COMPETITIVE EDGE
Customers are increasingly asking for eco-friendly products. Natural cork meets these expectations, enhancing your brand's image as responsible and environmentally conscious. Those who still ignore sustainable solutions risk losing customer trust and falling to the bottom of the list.
Cork mix is an eco-friendly choice because it contains no polyurethanes and is fully recyclable. When customers see that you prioritise sustainable solutions, you earn their trust. They know that choosing your products means caring for the environment, which keeps them coming back and recommending you to others.
#2 QUALITY THAT MAKES WORK EASIER
Cork mix is a clean, high-quality product that eliminates contamination and technical issues. Thanks to precise granulation, you can be confident that every component fits perfectly, ensuring smooth production without downtime. This allows you to focus on growing your business rather than troubleshooting technical problems.
What does this mean for your team? Production runs more smoothly because the material performs flawlessly. Orders are completed faster, leading to more satisfied customers. You have more time, take on more projects, and boost efficiency!
#3 CONSISTENCY IN PRODUCTION
Every defective batch means wasted time and money, while material inconsistency undermines customer trust in your brand. Ready-to-use, dry cork mix ensures consistency – delivering the same high production quality every time.
Pressure moulding allows you to return to projects with the next batch of mix and achieve identical shapes. The material's consistency guarantees that every component meets the same standards, with no need for adjustments or corrections.
Volume | 1 kg |
Application range | Pressure molding |
Colour | Natural |
Material | Natural cork |